第四章
陽(yáng)極放電隕石坑形成的建模
4.1. 介紹
在EDM中,材料的去除是通過快速重復(fù)發(fā)生的放電來(lái)實(shí)現(xiàn)的。在單個(gè)放電中,等離子體通道對(duì)放電點(diǎn)施加密集的功率密度,以誘導(dǎo)材料熔化和排出,然后在表面留下一個(gè)隕石坑(DiBitontoetal.,1989)。連續(xù)的排放電產(chǎn)生持續(xù)的材料去除,并產(chǎn)生由許多重疊的排放坑組成的加工表面。本研究旨在模擬隕石坑的形成過程,包括單個(gè)放電過程中材料的熔化、排出和再凝固。該模型可以提供在放電過程中的材料行為和隕石坑形成的見解。通過比較液體和液體-氣體混合介質(zhì)流體對(duì)隕石坑形成的影響,研究了濕的和近干燥的EDM。
建模工作集中在EDM精加工過程上。成品電火花加工通常具有負(fù)極性設(shè)置,以工件為負(fù)極。這種極性在短放電時(shí)間內(nèi)具有較低的陰極電極工具磨損(<3μs)(**查拉姆,1995)和陽(yáng)極表面光滑的隕石坑形態(tài)(Tamura和小林尊,2004年)。單個(gè)放電坑是陽(yáng)極表面EDM加工表面的主要特征。圖4.1(a)中顯示了一個(gè)示例。本研究開發(fā)的模型將能夠估計(jì)EDM精加工過程中放電中的陽(yáng)極材料行為。盡管陽(yáng)極和陰極都經(jīng)歷了快速的溫升并導(dǎo)致材料熔化,但人們發(fā)現(xiàn)它們具有不同的物質(zhì)排出機(jī)制,并產(chǎn)生不同的隕石坑形態(tài)(LuoandTao,2008)。
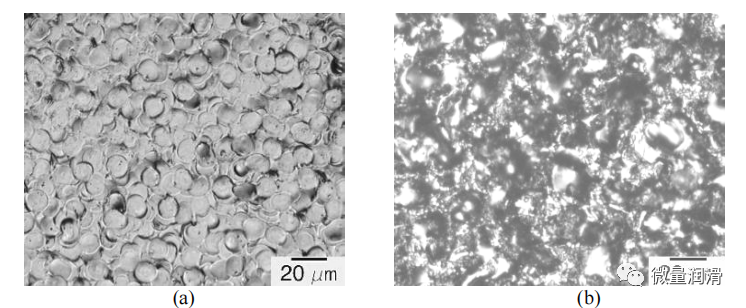
圖4.1。H13工具鋼的EDM表面,(a)負(fù)極顯示個(gè)別放電坑的明顯特征(放電電流即=1A、放電時(shí)間為=0.5μs、開路電壓和ui=210V)(b)表面粗糙(即=2A、ti=4μs和ui=210V)(電極:銅)。
放電過程中陽(yáng)極隕石坑的形成由兩相組成:等離子體加熱和氣泡坍塌。當(dāng)?shù)入x子體通道形成時(shí),介電流體破裂后,等離子體加熱階段開始。等離子體以高功率密度加熱電極,熔化陽(yáng)極材料,形成熔化池(DiBitontoetal.,1989)。用光譜儀測(cè)量到的等離子體通道中心的溫度很高,從4000K到8000K(Natsuetal.,2004)。等離子體通道充滿氣體混合,并隨著放電功率輸入而膨脹(Eubank等人,1993年)。等離子體通道的膨脹受到周圍介電流體的限制。等離子體內(nèi)部存在高壓。在放電結(jié)束時(shí),電源輸入停止。等離子體現(xiàn)在以氣泡的形式存在,它被周圍的流體壓縮并開始坍塌。氣泡的坍塌會(huì)影響熔體池,并導(dǎo)致熔融液體的飛濺(DiBitontoetal.,1989)。一些熔融的液體被噴射到周圍的電介質(zhì)流體中并被沖走。其余的部分分解并成為排放隕石坑的一部分。
在模擬等離子體加熱相和放電中的材料去除方面已經(jīng)進(jìn)行了相當(dāng)大的努力。DiBitonto等人。(1989)利用點(diǎn)熱源模型模擬了陰極材料的熔化。Patel等人。(1989)提出了一種擴(kuò)展熱源模型,其中采用具有時(shí)變加熱面積的高斯分布熱通量作為融化陽(yáng)極材料的熱源。Eubank等人。(Eubanketal.,1993)開發(fā)了一個(gè)可變質(zhì)量模型,能夠計(jì)算等離子體氣泡中的溫度和壓力。擴(kuò)展熱源分析(FEA)模型(Patel等人,1989年)采用有限元分析)模擬放電引起的工材料熔化、熱應(yīng)力、變形和微觀結(jié)構(gòu)變化(Murali和Yeo,2005年;Yeo等人,2007年;Das等人,2003年;Lasagni等人,2004年)。本研究采用擴(kuò)展熱源模型(Pateletal.,1989)。熱輸入可以用于預(yù)測(cè)電極和工作材料的熔融。材料去除是由于放電中等離子氣泡導(dǎo)致熔融材料飛濺(DiBitonto等人,1989;Patel等人,1989)。
關(guān)于等離子體泡的研究,謝瓦尼-塔巴等人。(2006)對(duì)放電氣泡動(dòng)力學(xué)進(jìn)行了數(shù)值分析,結(jié)果表明氣泡為在放電結(jié)束時(shí)被周圍的電介質(zhì)流體擠壓,并撞擊熔體池?;艨县惱锖屯匪梗?976)利用高速攝影技術(shù)對(duì)放電氣泡動(dòng)力學(xué)進(jìn)行了實(shí)驗(yàn)研究,表明材料的去除是由放電結(jié)束時(shí)液體介電射流的撞擊引起的。Klocke等人。(2007)測(cè)量了放電的力,并得出結(jié)論,氣泡坍塌產(chǎn)生了一個(gè)主要的沖擊力。??寺屯匪梗?960)利用Navier-斯托克斯方程從理論上推導(dǎo)出了放電氣泡動(dòng)力學(xué)。Tohi等人。(2002)采用霍普金森棒法測(cè)量了放電力,并與Eckman和威廉姆斯的理論結(jié)果(1960年)取得了良好的匹配。
據(jù)我們所知,目前還沒有一個(gè)同時(shí)包含等離子體加熱階段和氣泡坍塌階段的模型來(lái)模擬放電隕石坑的形成。本研究建立了一個(gè)包括材料熔融、氣泡壓縮和坍塌以及熔融材料飛濺和再凝固的模型。該模型是在流利的基礎(chǔ)上構(gòu)建的。對(duì)于等離子體加熱階段,該模型可以模擬熔化過程,并跟蹤遷移的熔體鋒面。潛熱效應(yīng)在以前的研究中沒有考慮到(Patel等人,1989;Murali和楊,2005;Yeo等人,2007;Das等人,2003),被納入本研究。對(duì)于氣泡坍縮階段,利用分?jǐn)?shù)體積(VOF)和熔融凝固模塊,模擬了多相相互作用、液體飛濺和液固轉(zhuǎn)化過程。
利用該模型模擬和比較了液體煤油濕電火花流體和煤油-空氣混合介電流體的放電和隕石坑形成。該模型還研究了不同水平的放電脈沖能量。下面幾部分將詳細(xì)解釋建模方法。仿真結(jié)果將給出,并將隕石坑的幾何形狀與實(shí)驗(yàn)測(cè)量結(jié)果進(jìn)行了比較。對(duì)氣泡初始?jí)毫M(jìn)行了參數(shù)研究,提高了對(duì)氣坑幾何形狀的預(yù)測(cè)精度。
4.2. 建模方法
以下兩部分介紹了等離子體加熱階段和氣泡坍縮階段的建模。
4.2.1. 等離子體加熱相
在接下來(lái)的章節(jié)中,從能量輸入、熱通量分布、初始和邊界條件、熔融和凝固建模以及材料特性等方面介紹了等離子體加熱階段的建模。
能量輸入:
加熱陽(yáng)極工件的能量Ea來(lái)自于放電脈沖能量Ed,其表示為:
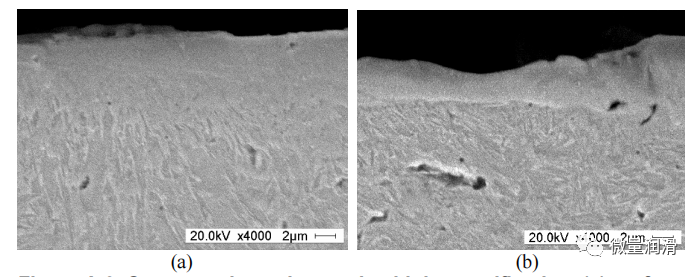
其中,即為放電電流,ue為放電電壓,ti為脈沖持續(xù)時(shí)間,η為對(duì)陽(yáng)極的能量分配因子。本研究采用Yeo等人使用的η=0.39。(2007)已被使用。
加熱陽(yáng)極的功率輸入,Qa(t),可表示為:

ie和ue是通過實(shí)驗(yàn)測(cè)量的。研究了三種EDM精加工條件,如圖4.2所示,并按其放電能的降序記為I、II和III。
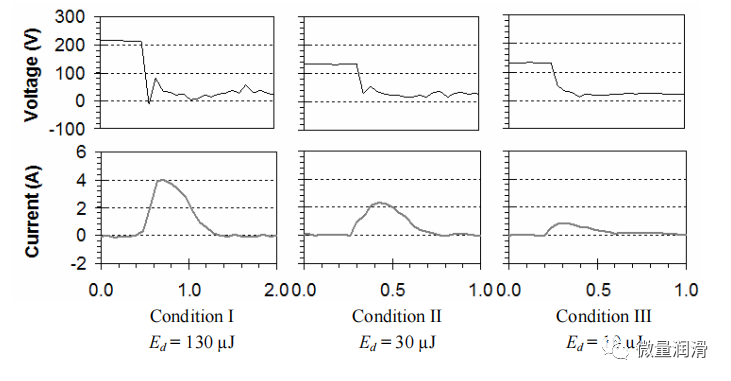
圖4.2。三種實(shí)驗(yàn)測(cè)量的放電條件下的放電波形。
熱通量分布:
基于擴(kuò)展熱源模型(Pateletal,1989),熱通量在等離子體通道中具有高斯分布,如圖4.3所示。距離等離子體柱中心距離的時(shí)變熱通量qa(r、t)表示為:

其中,qmax(t)為最大熱通量(在r=0處),rp(t)為陽(yáng)極表面等離子體加熱區(qū)域的半徑。假設(shè)一個(gè)柱狀等離子體,rp(t)是等于到等離子體的半徑。Rp(t)隨時(shí)間增長(zhǎng),由(Pateletal,1989)給出:

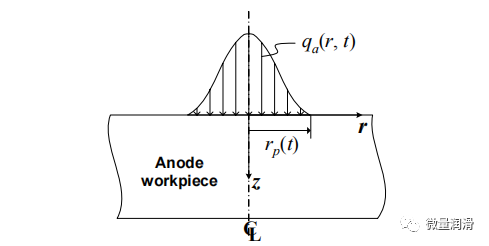
圖4.3。高斯分布熱通量的輪廓分布。
等離子體加熱區(qū)域上的熱通量Qa(r、t)的積分是加熱陽(yáng)極的總功率輸入Qa(t):

由于rp(t)和Qa(t)在特定時(shí)間內(nèi)已知,因此可以解決t、qa(r、t)。
模型示意圖、初始條件和邊界條件
該模型的軸度量原理圖如圖4.4所示。等離子體加熱相建模僅包括圖4.4中陽(yáng)極工件的區(qū)域,DFHG區(qū)域。陽(yáng)極區(qū)域沿r和z方向分別為100和80μm。該區(qū)域被分為0.05和0.05μm的網(wǎng)格(單元格)。
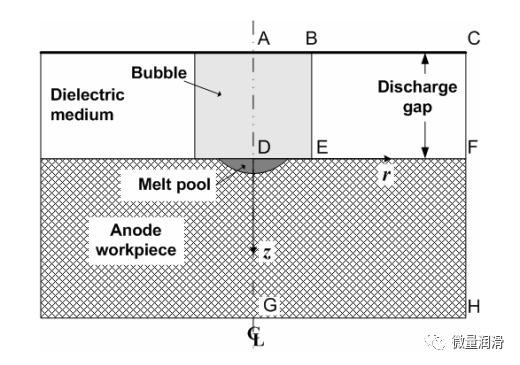
圖4.4。氣泡坍塌模型的示意圖。
工件的初始溫度Ti等于整個(gè)陽(yáng)極區(qū)域在t=0處的300K環(huán)境溫度T0。
在t>0時(shí),熱源被施加于陽(yáng)極表面,線DF。熱通量邊界條件可表示為:

其中,k為工件材料的導(dǎo)熱系數(shù)。FH和GH線的邊界條件(見圖。4),假定在恒溫t0下遠(yuǎn)離放電區(qū)域。
熔化和凝固:
利用流暢的熔融和凝固模塊來(lái)模擬材料在排放過程中的快速加熱和冷卻。采用焓孔隙率法(流利手冊(cè),2003)解決能量平衡和粘度問題熔化過程中的變化。熔體界面不會(huì)被明確地跟蹤熔體界面。相反,一個(gè)稱為液體分?jǐn)?shù)的量β,它表示細(xì)胞體積的分?jǐn)?shù),是基于焓平衡計(jì)算的。材料的總焓H由材料溫度變化引起的感焓h和相變引起的潛熱ΔH組成:

其中href為參考焓,Tref為參考溫度,L為材料的潛熱,β為液體分?jǐn)?shù)。工作材料,H13工具鋼,是一種合金材料。熔化涉及糊狀區(qū)(金屬手冊(cè),1980年),β可以表示為:

材料性能:
表4.1和4.2總結(jié)了H13工具鋼的材料性能。對(duì)于與溫度相關(guān)的特性,線性插值應(yīng)用于表中沒有規(guī)定的溫度水平。
表4.1年。H13工具鋼的恒定熱物理特性(Han等,2005;Childs等,2005)。

表4.2年。AISIH13工具鋼的溫度相關(guān)性導(dǎo)熱系數(shù)(金屬手冊(cè),1980)。

4.2.2. 泡沫破裂階段
在下面的章節(jié)中,從模型原理圖、初始和邊界條件、VOF建模和液體、固體和糊狀區(qū)域建模等方面介紹了氣泡坍縮階段的建模。
模型示意圖、初始條件和邊界條件
圖4.4顯示了氣泡坍塌模型的軸度量原理圖。除了在等離子體加熱階段中建模的陽(yáng)極區(qū)域DFHG外,氣泡在模型中還包括了(區(qū)域ABDE)、陰極表面(線AC)和介質(zhì)流體(區(qū)域BCFE)。與陽(yáng)極區(qū)域相同的0.05μm正方形網(wǎng)格(電池)是
作為氣泡坍縮相的初始條件的一部分,陽(yáng)離子區(qū)域DFHG中的溫度輪廓和熔體池的幾何形狀從等離子體加熱相導(dǎo)入。陰極,線交流,被簡(jiǎn)化為一個(gè)剛性和絕熱的邊界,與在陽(yáng)極表面上的溫度分布相同(線DF)。陰極與陽(yáng)極表面之間的垂直距離,即圖4.4中的放電間隙距離為20μm,通過測(cè)量沉模的EDM的實(shí)際切割深度和刀具磨損進(jìn)行實(shí)驗(yàn)確定。在所有調(diào)查的放電條件下的變化都小于10%。
柱狀氣泡,區(qū)域ABED,毗鄰陽(yáng)極熔體池。氣泡的初始半徑等于等離子體加熱相結(jié)束時(shí)的等離子體半徑,由方程4.4確定。氣泡充滿煤油蒸氣,建模為可壓縮理想氣體,其性能見表4.3。
表4.3年。煤油蒸氣、煤油液體和空氣的特性(流暢的6.3用戶指南,2006)。
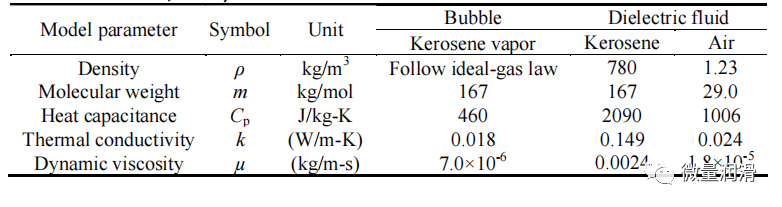
氣泡中的初始溫度設(shè)置為5000K(Natsuetal.,2004)。初始?xì)馀輭毫?00MPa,根據(jù)之前的研究屬于估計(jì)的范圍(Eubanketal.,1993;??寺屯匪?,1960),在第一組模擬中使用。因?yàn)樵跉馀輭毫烙?jì)中遇到了很大的變化(Eubanketal.,1993;??寺屯匪?,1960),第二組模擬研究了20MPa、200MPa、2GPa和20GPa四個(gè)水平的初始?xì)馀輭毫?duì)火山坑幾何形狀的影響。
BCFE區(qū)域充滿了電介質(zhì)流體。液體煤油和煤油-空氣混合物,由20%的煤油和80%的空氣組成,分別用于濕的和近干的EDM模擬。液體煤油和煤油-空氣混合物均被建模為不可壓縮相,性能見表3。假設(shè)介電流體區(qū)域的初始溫度呈指數(shù)衰減分布。在氣泡和介電流體界面(線BE)處,向介電流體分配5000K,并在邊界線CF處以指數(shù)級(jí)下降到環(huán)境溫度300K。邊界線CF設(shè)置為流向垂直于線CF的壓力入口。將邊界CF的初始?jí)毫υO(shè)置為初始?xì)馀輭毫?,并假設(shè)一旦氣泡坍塌,時(shí)間常數(shù)為10?8s,呈指數(shù)衰減。
VOF建模:
由于煤油蒸氣、空氣、煤油液、鋼和固體鋼五相,因此應(yīng)用VOF模塊分析它們的相互作用。VOF通過求解一組動(dòng)量方程和跟蹤每個(gè)相位的體積分?jǐn)?shù)來(lái)建模不混溶流體(或相位)(流暢的用戶指南,2006年)。這五個(gè)階段在模型中沒有互滲透。對(duì)于每個(gè)階段,q,在模型中,一個(gè)變量,aq,即計(jì)算單元中的相位體積分?jǐn)?shù),被分配到該階段。細(xì)胞中q相的體積分?jǐn)?shù)可以用以下三個(gè)條件之一:
aq=0,如果單元格空于階段q;
aq=1,如果單元充滿了第q階段;
0<aq<1,如果單元包含相q和一個(gè)或多個(gè)其他相之間的接口。
根據(jù)aq的局部值,細(xì)胞的密度、ρ和粘度μ以體積平均方式近似(流暢的用戶指南,2006),即,

動(dòng)量方程在整個(gè)計(jì)算單元中被求解,所得到的速度向量vv在相位之間共享。動(dòng)量方程依賴于細(xì)胞內(nèi)的體積平均密度ρ和粘度μ。力矩方程為(流利的用戶指南,2006年):

其中p為細(xì)胞中心的壓力,gv為重力加速度,F(xiàn)v為體積力。
能量方程與速度向量也在相位之間共享(流利的用戶指南,2006):

其中keff為體積平均有效導(dǎo)熱系數(shù),Sh為體積熱源。能量E和溫度T被視為質(zhì)量平均變量(流利的用戶指南,2006年):
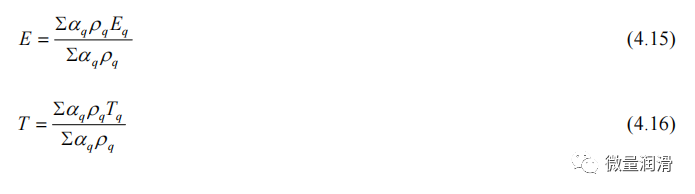
液體、固體和糊狀區(qū)域建模:
需要進(jìn)一步的努力來(lái)模擬在合金熔化階段共存的液體相、固體相和糊狀相。流體和固體型細(xì)胞很難合并在相同的分析領(lǐng)域,因?yàn)樗鼈兪怯貌煌脑順?gòu)建的。在本研究中,液相和固相都使用流體型電池進(jìn)行建模。Li等人提出的溫度依賴性粘度的方法。(2002),采用焓孔隙度和流利(流利用戶指南,2006)構(gòu)建的技術(shù),使固相和糊相建模成為可能。在溫度依賴性粘度法中,溫度低于溶劑體溫度的元素具有非常高的粘度(根據(jù)模擬穩(wěn)定性100到2000ns依賴于s/m)來(lái)模擬固體狀態(tài)。這樣,固體工作材料的流動(dòng)或運(yùn)動(dòng)非常小,其對(duì)建模精度的影響有限。如果材料溫度高于液相體溫度,則材料處于液相狀態(tài),并分配表1中所列的粘度值。
在溶液體和脂相體的溫度之間,即在糊狀區(qū),一個(gè)中間粘度可以用來(lái)模擬溶液體的狀態(tài)。流暢的焓孔隙率法可以更有效地處理液體和固體之間的過渡。它將糊狀區(qū)域視為一種多孔介質(zhì)(流暢的用戶指南,2006年)??紫堵时辉O(shè)置為等于該細(xì)胞中的液體分?jǐn)?shù)。因此,液體的比例更高分?jǐn)?shù),即更多的熔融液體,誘導(dǎo)更少的停滯來(lái)耗散流體流動(dòng)的動(dòng)量,即在糊狀區(qū)中液體和固體之間的相對(duì)運(yùn)動(dòng)。模糊區(qū)的動(dòng)量耗散,Md為(流暢的用戶指南,2006年):

其中β為液體分?jǐn)?shù),ε為完全凝固情況下防止除以零的少量數(shù)字,pvv為整個(gè)疇運(yùn)動(dòng)引起的固體速度矢量,Amush為無(wú)量綱糊狀區(qū)常數(shù)。較高的阿米什會(huì)導(dǎo)致較大的能量耗散。在本研究中,使用了Amush等于107(流利的用戶指南,2006)。
4.3. 仿真結(jié)果
4.3.1. 等離子體加熱相
圖4.5顯示了在放電條件III下,在0.5μs等離子體加熱階段,陽(yáng)極工作材料和固體組分上的溫度分布的模擬結(jié)果(圖4.2)??梢杂^察到,陽(yáng)極上的加熱面積隨著等離子體加熱時(shí)間的延長(zhǎng)而增加。0.1μs時(shí)的峰值溫度為10900K,0.5μs時(shí)降至3400K。峰值溫度的下降主要是由于等離子體通道的膨脹,這降低了放電功率密度,以及能量向周圍區(qū)域的耗散。

圖4.5。等離子體加熱階段的模擬。
圖4.5中的第二行圖顯示了表示其熔化和凝固狀態(tài)的工作材料的固體部分。在開始時(shí)(0.0μs),陽(yáng)極工作材料(圖4.5中的底部)具有100%固相。上部為非固相,它可以同時(shí)包含熔融液體和其他液相,包括氣泡和周圍的介電流體。在固相和液相之間有一個(gè)較薄的過渡帶,可以流暢地用于避免相的突變和相關(guān)的計(jì)算問題。過渡帶,約1μm厚,存在于所有相分?jǐn)?shù)結(jié)果的圖中。隨著溫度的升高,陽(yáng)極工件開始熔化,頂部形成的空腔表示熔體池的形成。熔體池的大小在0.4μs左右達(dá)到最大值。在那之后,增長(zhǎng)就停止了。0.5μs的熔體池大小略小于0.4μs。這與等離子體加熱階段的溫度下降有關(guān)。等離子體通道的膨脹將加熱功率密度降低到主要由傳導(dǎo)引起的散熱超過熱輸入的水平。在等離子體加熱階段,熔體池大小的收縮是對(duì)放電能量的浪費(fèi)。因此,等離子體加熱相的建模有可能應(yīng)用于優(yōu)化放電功率和持續(xù)時(shí)間,以提高材料的去除率和能源效率。
4.3.2. 泡沫破裂階段
圖4.6顯示了放電條件III的濕式EDM中氣泡坍塌階段的模擬結(jié)果。在模擬0.0、0.12、0.22、0.32、20.42 0.52 μs的時(shí)間步長(zhǎng)下,顯示了氣泡分?jǐn)?shù)、工作材料分?jǐn)?shù)和固體分?jǐn)?shù)的圖,描述了火山坑的形成過程。
如氣泡分?jǐn)?shù)所示,初始?xì)馀葜?.0μs時(shí),氣泡柱直徑為15μm,高度為20μm。由于溫度下降和周圍介質(zhì)流體的高壓,氣泡被迅速壓縮。在0.12μs時(shí),氣泡被壓縮到直徑小于5μm。當(dāng)介電流體穿透氣泡并將其分解成小塊時(shí),氣泡在0.22μs左右坍塌。氣泡的坍塌會(huì)對(duì)熔融池產(chǎn)生影響,并導(dǎo)致熔融的工作材料飛濺。
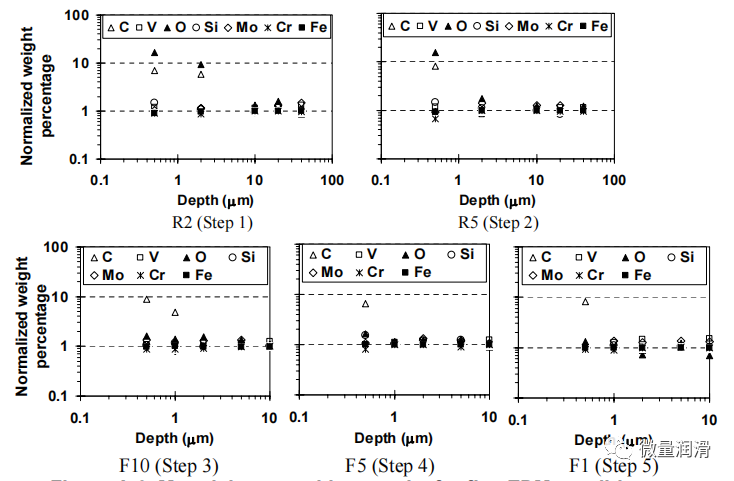
圖4.6。模擬了放電條件III下近濕EDM的氣泡坍縮階段。
在工作材料分?jǐn)?shù)的圖中,底部代表陽(yáng)極工作材料。在0.12μs時(shí),在氣泡坍塌之前,工作材料的熔融部分略有變形。在0.22μs時(shí),當(dāng)氣泡坍塌時(shí),沖擊會(huì)在熔體池的中心產(chǎn)生一個(gè)凹槽。熔融液體在0.32μs處攪拌并移向熔融池的一側(cè)。部分材料在0.42μs時(shí)開始從熔體池中分離。分離的物質(zhì)凝固成小液滴,變成噴出的碎片顆粒。其余的熔融材料沒有從沖擊中獲得足夠的動(dòng)量,分解成為隕石坑和EDM表面重新鑄層的一部分。
在固體組分的圖中,底部是固體(未熔體)工作材料,可以確定液相中的熔體池的空腔。在氣泡在0.22μs坍塌之前,通過空腔尺寸的減小可以觀察到熔融池的凝固。氣泡坍塌引起的沖擊使熔融物質(zhì)被取代,并在熔融池中引起強(qiáng)對(duì)流。噴射出的熔融物質(zhì)在0.32μs時(shí)開始凝固,在0.42μs時(shí)變成碎片滴。當(dāng)工材料分?jǐn)?shù)和固體分?jǐn)?shù)的輪廓相同時(shí),熔坑的最終形成表明熔融材料在0.52μs處完全凝固。
4.3.3. 模擬計(jì)算器
在排放條件I、II和III下,接近干燥和濕的EDM材料凝固后的隕石坑幾何形狀如圖4.7所示。初始?xì)馀輭毫υO(shè)置為2×108Pa。模型預(yù)測(cè)的隕石坑幾何形狀將與實(shí)驗(yàn)測(cè)量的隕石坑進(jìn)行比較,以進(jìn)行模型驗(yàn)證。
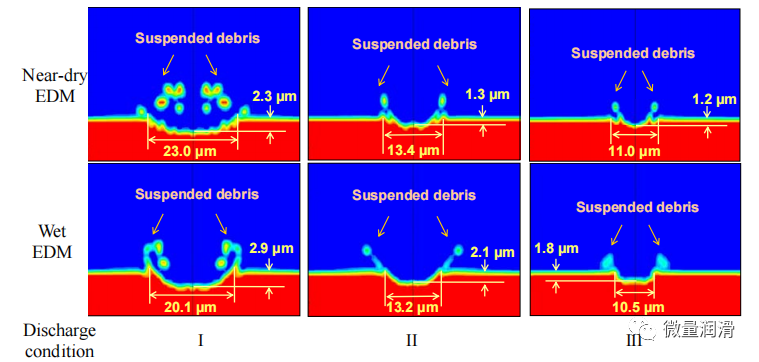
圖4.7。模擬了排放條件I、II和III條件下接近干燥和潮濕的EDM隕石坑的工材料分?jǐn)?shù)。
對(duì)于排放條件I、II、III,近干燥EDM坑直徑估計(jì)為23.0、13.4、11.0μm,濕EDM坑直徑估計(jì)為20.1、13.2、10.5μm。一般來(lái)說,近干的EDM的隕石坑直徑略大于濕的EDM。隕石坑深度則有相反的趨勢(shì),即近干燥EDM的隕石坑深度比干燥EDM的要淺。隕石坑的幾何形狀受介電流體的密度、粘度和導(dǎo)熱率的影響。濕EDM中煤油液體的高密度和粘度在壓縮氣泡時(shí)產(chǎn)生更大的動(dòng)量,并在氣泡坍塌時(shí)產(chǎn)生更大的影響。熔化材料被攪拌,比熔化池的EDM更深。因此,在濕EDM時(shí),隕石坑更深,直徑更小。
在放電條件I到III時(shí),隕石坑的直徑和深度隨著放電能量的減小而減小。隨著較低的放電能量來(lái)熔化的材料較少,熔化池的尺寸更小,最終隕石坑的大小減小。
4.4. 實(shí)驗(yàn)性水坑的產(chǎn)生和測(cè)量
我們進(jìn)行了實(shí)驗(yàn)來(lái)創(chuàng)建排放坑。隕石坑的大小和形狀是使用納米鏡iiia相原子力顯微鏡(AFM),使用j型掃描儀頭,0.4Hz掃描率和0.07μm分辨率的。將測(cè)量到的隕石坑幾何形狀與模型預(yù)測(cè)結(jié)果進(jìn)行了比較。
在不同的放電條件下,可以產(chǎn)生排放隕石坑。EDM過程創(chuàng)建了重疊的隕石坑,如圖4.1(a)所示,并且很難準(zhǔn)確地測(cè)量單個(gè)隕石坑的幾何形狀??梢岳脝未畏烹娺^程(Wong等,2003;Natsu等,2006),但放電間隙很?。╓ong等,2003),這與EDM條件不同。采用了一種被稱為稀疏連續(xù)放電(SCD)的新方法。
在SCD中,工件首先被拋光到鏡面,以確保小的排放坑可以與原始表面區(qū)分開來(lái)。對(duì)于10mmx10mm區(qū)域、H13陽(yáng)極工作材料和銅電極,放電間隙距離約為20μm,與連續(xù)放電條件下的間隙距離非常接近。在約2到3秒的放電后,可以在表面觀察到一簇稀疏分布的隕石坑以進(jìn)行分析。圖4.8顯示了使用放電條件II進(jìn)行接近干燥的EDM的隕石坑團(tuán)的一個(gè)例子。獲得了在大小和形狀上具有合理一致性的棘輪。因此,選擇有代表性的隕石坑進(jìn)行測(cè)量和分析。
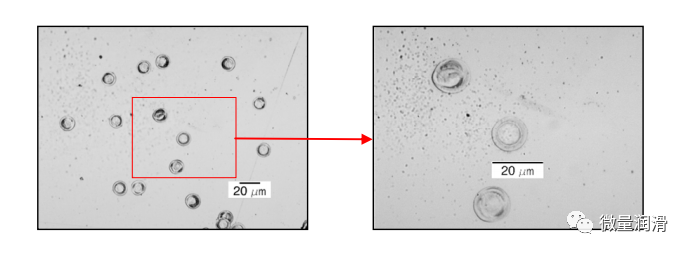
圖4.8。連續(xù)排放過程產(chǎn)生的排放坑(排放條件II的近干燥EDM)。
圖4.9顯示了在放電條件I、II和III下,在潮濕和接近干燥的EDM下產(chǎn)生的隕石坑的光學(xué)顯微圖、AFM3D圖像和橫截面。光學(xué)顯微鏡,AFM三維圖像是用于視覺評(píng)估隕石坑的形態(tài)。隕石坑的橫截面來(lái)自AFM數(shù)據(jù),并應(yīng)用于測(cè)量隕石坑的直徑和深度。
如圖4.9所示,從條件I到條件III,隕石坑的尺寸隨著放電能量的減小而減小。當(dāng)放電能量為130、30、10μJ時(shí),坑直徑約為20、13、10μm,坑峰深度約為2.0、0.4、0.1μm。從條件I到條件II和條件III,隕石坑深度顯著減少。對(duì)于排放條件II和III下的隕石坑,在隕石坑的中心可以觀察到一個(gè)凸起的底部。最明顯的是由接近干燥的EDM產(chǎn)生的隕石坑,可以簡(jiǎn)單地從三維圖像中識(shí)別出來(lái)。橫截面曲線顯示,在放電條件II和III中也存在類似的凸起底部。對(duì)于條件三,凸起的中心甚至可以上升到原來(lái)的表面水平以上,導(dǎo)致輕微的負(fù)深度。在EDM加工中,在加工表面上獲得良好的表面光潔度。
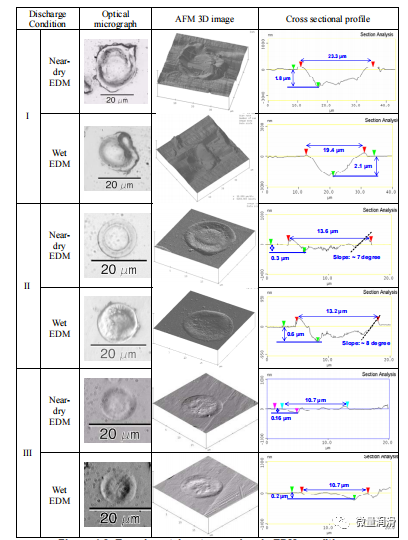
圖4.9。六種EDM條件下的實(shí)驗(yàn)隕石坑。
濕的和接近干燥的EDM產(chǎn)生不同的隕石坑,特別是在高放電能量的情況下,條件I。接近干燥的EDM隕石坑的直徑更大(23μmvs. 18 μm)和更小的深度(1.8μmvs.2.3μm)。在相同的EDM條件下,在接近干燥的EDM中創(chuàng)建了一個(gè)相對(duì)平坦的隕石坑,這更適合完成EDM,如上章所述。隕石坑的直徑和深度與不同的介電介質(zhì)流體性質(zhì)有關(guān)。在接近干燥的EDM中使用的煤油-空氣混合物由于被空氣稀釋,其粘度和密度較低。當(dāng)壓縮氣泡時(shí),它產(chǎn)生的動(dòng)量更小,從而使氣泡坍塌的沖擊力更小。
隨著脈沖能量的減小,近干和濕電火花處理的隕石坑幾何差異不那么明顯。對(duì)于條件II,幾乎干燥的EDM產(chǎn)生的隕石坑稍淺,深度約為0.3μm。在條件III中,近干燥和潮濕EDM的隕石坑幾何形狀沒有顯著差異。較小的放電能量降低了氣泡坍塌的沖擊力。因此,熔融材料獲得較少的動(dòng)量來(lái)克服熔融池的表面張力。由于表面張力對(duì)低脈沖能量EDM起著更大的作用,濕EDM的高沖擊力不足以比濕EDM產(chǎn)生更深的隕石坑。
4.5. 比較與討論
圖4.10比較了模型預(yù)測(cè)和實(shí)驗(yàn)測(cè)量的排放坑的直徑和深度。該模型對(duì)隕石坑直徑的預(yù)測(cè)提供了良好的預(yù)測(cè),與實(shí)驗(yàn)的平均值偏差小于10%。它捕捉到了實(shí)際的隕石坑形成的特征。圖4.8和4.9中的模型和真實(shí)隕石坑分別顯示了山脊的特征底部有凸起的隕石坑。該模型區(qū)分了近干和濕EDM產(chǎn)生的隕石坑,并預(yù)測(cè)了隨著隕石坑能量減小而減小的趨勢(shì)。然而,該模型并不能準(zhǔn)確地估計(jì)條件II和條件III中的淺層隕石坑深度。
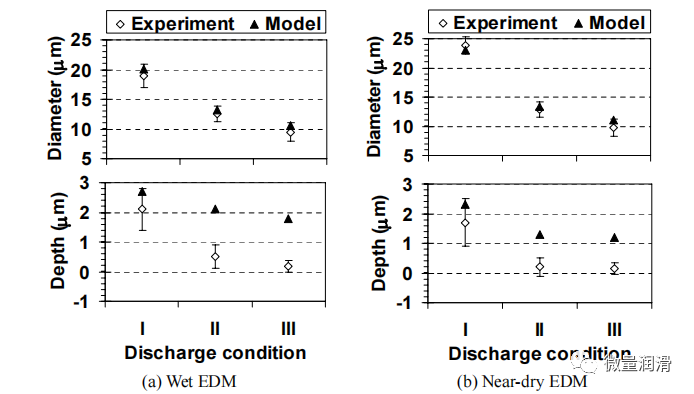
圖4.10。實(shí)驗(yàn)坑和模擬隕石坑的尺寸比較。
這個(gè)模型往往會(huì)高估了隕石坑的深度。對(duì)于脈沖能量相對(duì)較高、130μJ的條件I,模擬的隕石坑深度在實(shí)驗(yàn)變化的上部范圍內(nèi)。當(dāng)條件II和條件III的放電能量分別下降到30和10μJ時(shí),實(shí)驗(yàn)測(cè)量的隕石坑深度減少到1μm以下,隕石坑的一些凸起部分甚至上升到原來(lái)的表面水平以上。在這些情況下,模擬的隕石坑都深于1.2μm。
對(duì)隕石坑深度的高估可以歸因于幾個(gè)原因。首先,如果冷卻速率超過臨界值,固化金屬的比體積可以增加,即材料體積會(huì)擴(kuò)大(里德-希爾和阿巴斯欽,1994)。根據(jù)模擬估計(jì),排放坑形成過程中遇到的冷卻速率高于109K/s。這種快速的冷卻速率已經(jīng)超過了金屬合金的臨界值,通常為105K/s(里e德-Hill和阿巴斯基安,1994年)。因此,鋼工料在排放后的凝固過程中預(yù)計(jì)會(huì)膨脹。擴(kuò)大的體積占據(jù)了隕石坑中更多的空間,并減少了隕石坑的深度。
其次,熔體池的深度可能被高估了。對(duì)實(shí)際熔體池深度的粗略估算是總結(jié)條件II和III測(cè)量的隕石坑深度分別小于0.9和0.4μm,條件II和III連續(xù)開采的重鑄層厚度分別小于1.7和1.5μm。雖然由于連續(xù)EDM中多個(gè)重鑄層可能重疊,這導(dǎo)致了高估,但推導(dǎo)出的池深度(條件II和條件III分別為2.6和1.9μm)仍然小于模擬結(jié)果(條件II和條件III分別為2.7和2.2μm)。
第三,模擬中的初始?xì)馀輭毫κ遣淮_定的。在模擬中,所有放電條件下的初始?xì)馀輭毫鶠?×108Pa。由于氣泡壓力的累積與放電脈沖能量有關(guān),因此實(shí)際壓力應(yīng)發(fā)生變化。更高的能量預(yù)計(jì)會(huì)更劇烈地膨脹氣泡,從而導(dǎo)致更高的初始?xì)馀輭毫?,從而在放電結(jié)束時(shí)產(chǎn)生更強(qiáng)的壓縮。為了克服缺乏精確的氣泡壓力,下一節(jié)將進(jìn)行研究,以研究初始?xì)馀輭毫?duì)隕石坑形成的影響。
4.6. 初始?xì)馀輭毫Φ挠绊?/strong>
模擬是在2×107、2×108、2×109和2×1010Pa的初始?xì)馀輭毫ο逻M(jìn)行的,在排放條件I、II和III下。結(jié)果如圖4.11所示。
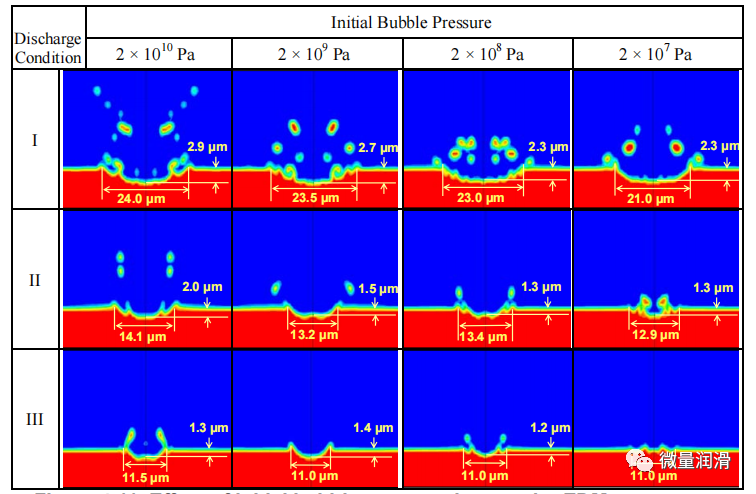
圖4.11。三種放電條件下接近干燥EDM的初始?xì)馀輭毫?duì)隕石坑幾何形狀的影響。
在圖4.11中,模擬的氣坑直徑和深度隨著初始?xì)馀輭毫Φ脑黾佣龃蟆?duì)于條件I、條件II和條件III,當(dāng)初始?xì)馀輭毫?×107增加到2×1010Pa時(shí),隕石坑直徑和深度增加的百分比分別為14%、9%和5%和26%、50%和30%。初始?xì)馀輭毫Φ淖兓瘜?duì)隕石坑深度的影響較大。此外,在碎片噴射更廣泛的高壓情況下,碎片噴射擴(kuò)散更劇烈。
比較模擬氣坑和真實(shí)氣坑,2×108Pa的初始?xì)馀輭毫κ菞l件I和條件II對(duì)隕石坑直徑和深度最接近的預(yù)測(cè)。對(duì)于條件III,2×107Pa的壓力在模擬和真實(shí)的隕石坑剖面中產(chǎn)生了很好的匹配(圖4.9,具有條件III的接近干燥的EDM)。在這兩個(gè)剖面中,側(cè)面略微向下滑動(dòng),而中心向上膨脹并上升到原來(lái)的表面水平以上。在那個(gè)模擬中沒有發(fā)生物質(zhì)噴射。
在放電條件I和排放條件II中,改變初始?xì)馀輭毫Σ⒉荒芨纳茖?duì)氣坑深度的預(yù)測(cè)。氣泡壓力并不是導(dǎo)致模型高估隕石坑深度的主要因素。第5節(jié)討論的材料體積膨脹和對(duì)熔體池深度的高估是提高模型精度需要解決的主要問題。
模型的改進(jìn)可以預(yù)期如下。首先,應(yīng)該對(duì)在本研究中使用文獻(xiàn)值的等離子體加熱階段的模型參數(shù)進(jìn)行修正,以更好地?cái)M合低放電能量(小于100μJ)的情況。其次,需要通過實(shí)現(xiàn)一個(gè)將材料比體積的變化與其冷卻速率相關(guān)聯(lián)的經(jīng)驗(yàn)數(shù)據(jù)庫(kù),將材料在高冷卻速率下的膨脹因素包括在內(nèi)。此外,另一個(gè)潛在的進(jìn)展是納入氣泡膨脹的建模。這樣,就可以利用更準(zhǔn)確的氣泡壓力,而不是使用文獻(xiàn)值。挑戰(zhàn)在于,氣泡膨脹模型需要兩種可壓縮的流動(dòng),一種用于蒸汽氣泡,另一種用于周圍的介電流體。目前,這種情況對(duì)于流利的和其他CFD軟件是不可行的。
4.7. 結(jié)論性言論
本研究證明了陽(yáng)極電極上放電坑形成的模型?;诘入x子體加熱模型的研究進(jìn)展(Pateletal.,1989),本研究開發(fā)的模型可以通過考慮潛熱來(lái)處理材料的熔融和凝固。該模型進(jìn)一步結(jié)合了氣泡坍塌相來(lái)模擬介質(zhì)流體、氣泡、熔融材料和固體工件之間的多相相互作用。通過比較實(shí)驗(yàn)測(cè)量的隕石坑直徑和深度,利用流利的軟件對(duì)排放隕石坑形成過程進(jìn)行建模是可行的。
實(shí)驗(yàn)驗(yàn)證采用SCD進(jìn)行,可以更好地模擬實(shí)際的EDM過程。模擬產(chǎn)生了真實(shí)的隕石坑形態(tài),如堆積的火山峰和凸起的底部。該模型對(duì)隕石坑直徑提供了很好的預(yù)測(cè)效果。實(shí)驗(yàn)和模擬結(jié)果表明,使用煤油空氣的近干燥EDM比使用液體煤油的濕EDM產(chǎn)生更大但更淺的排放坑。該模型追蹤了隨著放電能量的減小,隕石坑尺寸減小的趨勢(shì)。燈泡壓力的初始條件對(duì)模擬精度有一定的影響。初始?xì)馀輭毫υ?07到108Pa之間,適合于模擬與實(shí)驗(yàn)相匹配的火山坑幾何形狀。初始?xì)馀輭毫υ降?,放電脈沖能量就越低。
該模型被發(fā)現(xiàn)高估了隕石坑的深度。其原因是初始?xì)馀輭毫斎氩粶?zhǔn)確,高估了熔體池的深度,并忽視了高冷卻速率下的材料體積膨脹。通過修正等離子體加熱相模型來(lái)改進(jìn),更好地估計(jì)熔體池的大小和通過結(jié)合冷卻速率對(duì)材料比體積的影響。
第五章
結(jié)論及未來(lái)工作
本研究對(duì)下一代EDM過程的持續(xù)發(fā)展做出了貢獻(xiàn)。通過實(shí)驗(yàn)探索和工藝建模,對(duì)干燥和近干的電火花壓磨過程進(jìn)行了研究。
5.1. 主要貢獻(xiàn)
本研究的主要貢獻(xiàn)有兩個(gè)領(lǐng)域:
綜合干法和近干法EDM銑削工藝開發(fā)
利用氣體和液體混合物作為非規(guī)介電介質(zhì)和旋轉(zhuǎn)管狀工具電極內(nèi)部沖洗介質(zhì)流體,證明了干燥和接近干燥的EDM銑削工藝的可行性。
氧輔助干式EDM研磨被證明是一種理想的EDM粗加工工藝,能夠?qū)崿F(xiàn)高M(jìn)RR,快速氧化被認(rèn)為是其增強(qiáng)MRR的機(jī)理。
采用能源部研究氧輔助干EDM粗糙加工過程。確定了關(guān)鍵的放電參數(shù)及其影響。
近干燥的EDM研磨工藝是EDM精加工的理想選擇,并通過廣泛的實(shí)驗(yàn)研究對(duì)介質(zhì)流體、電極材料和放電參數(shù)的影響進(jìn)行了分類。
采用干EDM粗糙加工和近干EDM光潔度加工的綜合工藝,可以實(shí)現(xiàn)0.09μmRa的鏡面表面光潔度。這可能是PMDEDM工藝在超細(xì)表面表面加工中的潛在升級(jí),可以降低介質(zhì)流體成本和環(huán)境問題。
陽(yáng)極放電隕石坑形成的建模
建立了陽(yáng)極電極上放電坑形成模型。對(duì)介質(zhì)流體、氣泡、熔融材料和固體工件之間具有復(fù)雜多相相互作用的氣泡坍塌相進(jìn)行了建模。
通過與實(shí)驗(yàn)測(cè)量的隕石坑直徑和深度的比較,證明了使用流利的軟件構(gòu)建的模型是可行的。
應(yīng)用該模型證明了近干式電火花加工比濕式電火花加工在產(chǎn)生平滑的隕石坑和更好的表面光潔度方面的優(yōu)點(diǎn)。
對(duì)干燥和近干EDM磨削工藝的研究為探索非常規(guī)EDM介質(zhì)介質(zhì)和實(shí)現(xiàn)EDM銑削配置開辟了一個(gè)領(lǐng)域。對(duì)排放隕石坑建模的努力為模擬更真實(shí)的排放隕石坑提供了機(jī)會(huì),使其能夠更好地理解材料在EDM中的去除機(jī)制,從而實(shí)現(xiàn)更好的過程預(yù)測(cè)、控制和優(yōu)化。
5.2. 對(duì)未來(lái)研究的建議
通過本研究的探索性工作,可以建議在干、近干EDM過程優(yōu)化和EDM過程建模領(lǐng)域進(jìn)行一些未來(lái)的研究。
研究可以繼續(xù)利用液體-氣體介質(zhì)流體進(jìn)行接近干燥的EDM。一方面,可以測(cè)試新的液體和氣體含量,以提高加工性能和加工表面改性。例如,由于發(fā)現(xiàn)快速氧化有利于高M(jìn)RR,可以用促進(jìn)氧化的介質(zhì)制備和測(cè)試EDM粗糙過程。具有特殊材料組合物的電介質(zhì)和電極可用于表面合金化和改性。Yan等人也成功地進(jìn)行了類似的實(shí)踐。(2005),Wang等人。(2002)和Mohri等人。(1993)在常規(guī)的濕式電火花加工工藝中。考慮到不同的混合液體和氣體液體的靈活性,在接近干燥的EDM中,這是值得探索的潛力。另一方面,由于液體氣體百分比對(duì)加工性能有可觀察的影響,可以使用更精確的流量控制的更好的液體氣體分配器進(jìn)行表征,從而可以通過根據(jù)加工要求定制液體氣體百分比來(lái)定制工藝。
對(duì)于近干燥電火花磨加工的精度應(yīng)用,需要更多的磨損表征和補(bǔ)償。由于高電極磨損比,>50%為當(dāng)前更好的整理操作,作為EDM的自然發(fā)生,該檢測(cè)、預(yù)測(cè)和補(bǔ)償?shù)毒吣p的算法和系統(tǒng)對(duì)于EDM銑削的成功應(yīng)用至關(guān)重要。為此目的,可能需要一種在線放電脈沖監(jiān)測(cè)系統(tǒng)和一種自適應(yīng)控制算法。工件和工具電極上的材料去除是通過單個(gè)放電來(lái)實(shí)現(xiàn)的,因此,放電脈沖的數(shù)量應(yīng)與工具的磨損量相關(guān)。此外,每個(gè)脈沖的材料去除量隨放電參數(shù)設(shè)置、工件和電極材料組合甚至放電條件而變化。因此,一種可能基于半經(jīng)驗(yàn)的、能夠適應(yīng)不同加工條件的算法將具有很大的價(jià)值,可以良好地預(yù)測(cè)每個(gè)脈沖的材料去除情況,從而準(zhǔn)確地預(yù)測(cè)和補(bǔ)償電極磨損。
并建議進(jìn)一步補(bǔ)充和擴(kuò)展隕石坑形成模型。單個(gè)隕石坑形成模型被認(rèn)為是利用通過模擬獲得的碎片粒子和真實(shí)的隕石坑幾何形狀來(lái)幫助實(shí)現(xiàn)連續(xù)EDM過程建模的潛力。在連續(xù)EDM中,連續(xù)放電取決于電場(chǎng)分布,并在經(jīng)歷更高場(chǎng)強(qiáng)的點(diǎn)啟動(dòng)。電場(chǎng)受放電間隙的碎片分布以及陽(yáng)極和陰極表面形態(tài)的影響,因?yàn)椴迦腚妶?chǎng)的突然幾何形狀會(huì)導(dǎo)致電場(chǎng)失真局部加強(qiáng)場(chǎng),它們被認(rèn)為是決定連續(xù)放電位置和條件(火花、電弧或短路)的主要因素(Luo,1997)。因此,通過利用模擬的隕石坑幾何形狀來(lái)更新加工表面的形貌,并利用模擬的碎片顆粒來(lái)計(jì)算碎片的分布通過循環(huán)流化法計(jì)算或統(tǒng)計(jì)分析,可以模擬每次放電后的電場(chǎng)分布,以確定以下放電的位置和可能的條件(火花、電弧或短路)。因此,放電位置的拓?fù)浣Y(jié)構(gòu)可以通過隕石坑幾何形狀的幾何變形來(lái)更新,并根據(jù)放電條件(火花、電弧或短路)可以分為不同的形狀。改變這一過程,可以模擬一個(gè)連續(xù)的電火花加工過程,能夠預(yù)測(cè)材料去除率(MRR)和加工表面形貌。
這些建議的未來(lái)主題都可用于進(jìn)一步提高對(duì)EDM過程的理解和控制,并有助于以更低的成本提高EDM的生產(chǎn)率和質(zhì)量。
附錄
EDM表面和地下特性的表征
A.1. 介紹
在EDM中,放電點(diǎn)經(jīng)歷了一個(gè)快速的熔化和分解循環(huán),使EDM加工表面留下一層熱影響區(qū)。EDM表層的微觀結(jié)構(gòu)、化學(xué)成分和力學(xué)性能不同于襯底材料。
在熱影響區(qū)域的最頂部是再鑄層,它由再固化材料組成。重鑄層的形成在時(shí)間和空間域上都經(jīng)歷了高溫梯度。它使重鑄層具有極細(xì)、致密的微觀結(jié)構(gòu)和拉伸熱應(yīng)力。高熱應(yīng)力可引起孔隙性和微裂紋(AbuZeid,1997)。這些表面缺陷會(huì)導(dǎo)致應(yīng)力集中,降低機(jī)械加工部件的機(jī)械性能和抗疲勞性。在高溫化學(xué)反應(yīng)和4000~8000K下(Natsuetal.,2004),從而改變了EDM表面的化學(xué)組成。在切割碳鋼方面,克魯斯等人。(1995)觀察到使用時(shí)重鑄層的碳含量增加(約4倍)碳?xì)浠衔锝橘|(zhì);而使用水介質(zhì)時(shí)碳含量下降(高達(dá)50%)。鋼中碳含量的變化會(huì)影響其力學(xué)性能,如韌性、表面摩擦系數(shù)和韌性。Kulkarni等人。(2005)檢測(cè)去電處理過程中氫向工件的擴(kuò)散,這會(huì)降低鋼的延性,并導(dǎo)致材料過早失效(Gabe,2001)。Soni等人。(1996)證實(shí)了材料從工具電極遷移到工件的存在。
因此,表征加工表面特性是全面了解干燥和近干電火花加工銑削過程的理想條件。本研究努力考察了EDM表面的重鑄層、顯微硬度、材料成分和殘余應(yīng)力。
A.2. 實(shí)驗(yàn)設(shè)置
研究了第三章在五種不同干燥和接近干燥的EDM條件下R2、R的表面、R5、F15、F5和F1的表面(表3.3)。前兩個(gè)加工步驟(R2、R5)是氧輔助干式EDM,以下三個(gè)步驟(F10、F5、F1)是使用煤油-空氣混合物的接近干式EDM精加工。
A.2.1. 樣品制備
調(diào)查中使用的工件材料為DMD沉積的H13工具鋼。研究了機(jī)加工表面的頂部和地下表面的性能。在機(jī)械加工后,對(duì)頂部表面進(jìn)行正常檢查。地下表面的性質(zhì)是由查看已加工表面的橫截面。樣品用金剛石鋸軸向切片,頂部表面涂上鎳,并用環(huán)氧樹脂安裝。鎳涂層有助于保存頂部脆性重鑄層,否則在之前拋光過程中容易剝離。橫截面拋光從400網(wǎng)格的砂紙開始,逐漸下降到2400網(wǎng)格,然后用1μm氧化鋁懸浮液進(jìn)行精細(xì)拋光。然后用乙醇稀釋的5%硝酸進(jìn)行化學(xué)蝕刻,揭示了材料的微觀結(jié)構(gòu)。
A.2.2. 分析設(shè)備及程序
使用奧林巴斯PME3光學(xué)顯微鏡和飛利浦XL30FEG掃描電子顯微鏡(SEM)觀察重鑄層。檢查機(jī)加工表面的頂部和橫截面。
顯微硬度分析采用MTS納米插入中心II壓痕設(shè)備進(jìn)行。施加2000μN(yùn)的壓痕力,其深度約為100nm,大小約為1μm。沿3×6的橫截面進(jìn)行凹痕,垂直6步,橫向3次重復(fù)。第一個(gè)縮進(jìn)在頂表面下方約2μm,R2和R5表面的垂直增量為15μm,F(xiàn)10表面的垂直增量為7μm。對(duì)于F5和F1表面,重鑄層很薄(<1.5μm),很難將凹痕直接放在層內(nèi)以獲得一致的測(cè)量值。因此,在F5和F1表面的頂部表面上進(jìn)行壓痕,以達(dá)到重鑄層的顯微硬度。
材料組成采用EDAX能量色散法進(jìn)行了分析光譜鏡(EDS)與EEM連接到飛利浦XL30FEG。首先確定材料中可能存在的元素,并從材料光譜中近似出每個(gè)元素的重量百分比。首先分析基材的成分,并作為參考值使用。計(jì)算結(jié)果如表所示A.1.然后檢查加工表面和地下的組成,每個(gè)元素的重量百分比除以表中的參考值A(chǔ).1,以獲得每個(gè)元素的標(biāo)準(zhǔn)化權(quán)重百分比。因此,材料成分的減少和增加分別由歸一化重量百分比低于1和高于1表示。
表A.1。EDS測(cè)量中DMDH13的材料組成。
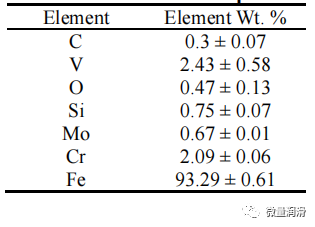
表面殘余應(yīng)力分析采用Bruker發(fā)現(xiàn)D8X射線衍射(XRD)系統(tǒng)進(jìn)行。應(yīng)用最廣泛的sin2ψ方法作為一種應(yīng)力評(píng)價(jià)的無(wú)損方法(培養(yǎng)力,1959)。
在XRD應(yīng)力測(cè)量中,伴隨殘余應(yīng)力的應(yīng)變使晶格平面扭曲,導(dǎo)致晶格間距d的變化,從而改變了應(yīng)用x射線時(shí)材料的衍射天使2θ。對(duì)于應(yīng)力表面,2θ天使隨不同的x射線入射角ψ而變化。根據(jù)彈性理論(Saada,1993),2θn和2θi之間的差值,即衍射角在正態(tài)方向(ψ=0)和傾斜方向(ψ=ψ)分別與表面應(yīng)力σφ有關(guān)系,如圖a.1所示。因此,與關(guān)系開始

其中,K為應(yīng)力因子,E為測(cè)試材料的楊氏模量,ν為測(cè)試材料的泊松比,θ為非應(yīng)力材料的衍射天使,通過在標(biāo)稱方向和傾斜方向上應(yīng)用x射線測(cè)量可以得到σφ。

圖A.1。XRD殘余應(yīng)力測(cè)量示意圖(文化度,1959年)。
在殘余應(yīng)力測(cè)量中,由于其他表面是粗糙的,可以向發(fā)散的方向衍射入射的x射線,從而引入額外的測(cè)量噪聲。如果需要對(duì)這些粗糙的表面進(jìn)行精確的測(cè)量,則應(yīng)采用XRD以外的方法。
A.3. 實(shí)驗(yàn)結(jié)果
A.3.1. 堆疊層觀測(cè)
重鑄層在快速熔融凝固過程中形成,通常具有脆性,具有熱應(yīng)力引起的微裂紋。根據(jù)應(yīng)用程序的不同,需要進(jìn)行后期處理來(lái)去除重鑄層,有時(shí)還會(huì)去除它下面的熱影響區(qū)域,以避免它可能產(chǎn)生的有害影響。
圖A.2顯示了從粗糙到表面的5個(gè)表面(R2、R5、F10、F5和F1)的橫截面和頂視圖。從橫截面開始,重鑄層與基材區(qū)別為頂部的白色層?;A(chǔ)材料中的白色和灰色對(duì)比度顯示了DMDH13工具鋼中兩種不同相,馬氏體和奧氏體的微觀結(jié)構(gòu)(Ghosh和Choi,2006)。與基材的微觀結(jié)構(gòu)相比,在重鑄層中沒有觀察到明顯的微觀結(jié)構(gòu)模式,因?yàn)樵诘?章的層形成過程中觀察到的快速冷卻速率高于109K/s,阻礙了微觀結(jié)構(gòu)的生長(zhǎng)和發(fā)展。較短的排放持續(xù)時(shí)間,小于2μs,允許一個(gè)極短的加熱周期和相應(yīng)的較短的冷卻周期,這抑制了微觀結(jié)構(gòu)的生長(zhǎng)。過冷的液體金屬表現(xiàn)出非晶玻璃結(jié)構(gòu)(里德希爾和阿巴斯基安,1994),因此它可以是重鑄層的微觀結(jié)構(gòu)。為了確定精確的微觀結(jié)構(gòu),透射電子顯微鏡(TEM)可以用來(lái)分析重鑄材料的衍射模式。
圖A.4顯示了測(cè)量的重新鑄層厚度。從第一步粗糙加工工藝到最終精加工工藝,重鑄層厚度從14±4μm到1.5±0.2μm。重鑄層在過渡過程中變得更薄、更平滑。這與較低的放電能量產(chǎn)生較淺的放電坑和更好的表面光潔度是一致的。
此外,從圖A.2的頂部視圖中可以看出,從粗糙操作到完成操作,表面特征變得越來(lái)越細(xì)。在由R2(步驟1)和R5(步驟2)加工的表面中,由于強(qiáng)熱應(yīng)力,很容易觀察到微裂紋。對(duì)于F10(步驟3)機(jī)加工表面,可見的微裂紋已大大減少。微裂紋不再是重鑄層表面的主要特征。對(duì)于F5(步驟4)和F1(步驟5)的最后兩個(gè)修整步驟,具有可區(qū)分的各個(gè)排放坑,無(wú)裂紋跡象。低放電功率密度降低了溫度梯度和熱應(yīng)力,從而有助于緩解表面的缺陷。
一般來(lái)說,在從粗糙加工到完成EDM加工過程的重鑄層形態(tài)方面,可以觀察到更好的表面完整性和對(duì)EDM過程的影響更小。
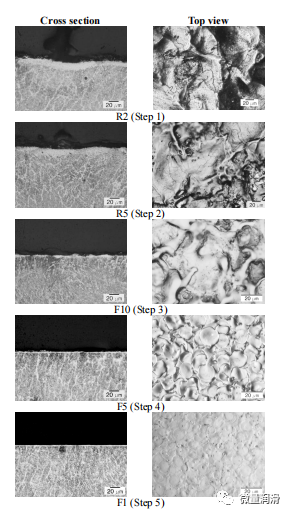
圖A.2。EDM曲面的剖面圖和頂視圖。
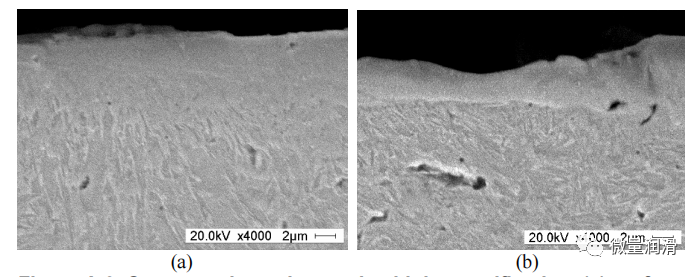
圖A.3。在高倍率下觀察到的橫截面,(a)步驟2產(chǎn)生的表面和(b)步驟3產(chǎn)生的表面。
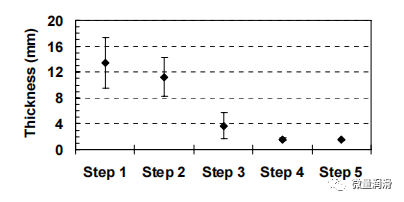
圖A.4??偨Y(jié)了不同加工步驟的重鑄層厚度。
在重鑄層下,已經(jīng)報(bào)道了對(duì)熱影響區(qū)的觀察結(jié)果(Bleesetal.,2006)。熱影響區(qū)是指該層在放電過程中經(jīng)歷了“熱處理”,但不經(jīng)過熔融和凝固循環(huán)。據(jù)報(bào)道,它的微觀結(jié)構(gòu)比基礎(chǔ)材料更精細(xì)。然而,在所研究的表面中沒有觀察到微觀結(jié)構(gòu)的明顯尺寸轉(zhuǎn)變,如圖A.3所示。這可能是因?yàn)榈头烹姵掷m(xù)時(shí)間(所有五個(gè)加工步驟都不超過5μs)不允許熱量深入穿透并改變微觀結(jié)構(gòu)。然而,僅僅從微觀結(jié)構(gòu)的觀察來(lái)看,要說EDM過程的影響僅限于重鑄層還不夠明顯。
對(duì)顯微硬度和材料組成的評(píng)價(jià)有助于進(jìn)一步揭示其表面和地下的性能。
A.3.2. 納米壓痕
納米壓痕在工件的橫截面上進(jìn)行。GPa的顯微硬度與距離頂表面的距離如圖A.5所示?;娘@微硬度約為4.5~5.0GPa。
對(duì)于R2加工的表面(步驟1),在頂表面附近的峰值硬度非常高,約為11GPa。向基底過渡時(shí),冷卻速率和合金化的影響減小,硬度值逐漸降低。顯微硬度恢復(fù)到頂部表面下45μm的基礎(chǔ)材料水平。由于重鑄層約為9~17μm(圖A.4),這表明隨著顯微硬度的增加,確實(shí)存在熱影響區(qū),但使用硝酸蝕刻劑看不到。
對(duì)于R5加工的表面(步驟2),峰值顯微硬度大致相同(11GPa),但高顯微硬度深度降低到16μm以下,略大于重鑄層厚度(圖A.4)。
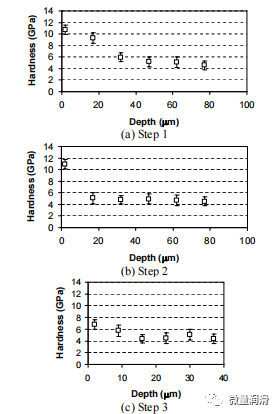
圖A.5。加工步驟R2、R5和F10的顯微硬度測(cè)量。
對(duì)于成品EDM加工F10(步驟3),峰值硬度增加(至7GPa)和硬化層深度(約10μm)不高。
對(duì)于由F5和F1已加工的表面(步驟4和5),納米凹痕直接應(yīng)用于已加工表面的頂部。F5和F1表面的重鑄層顯微硬度分別為9.3±2.9和9.1±1.5GPa。表面加工時(shí)重鑄層的平均顯微硬度較高。測(cè)量的變化大于橫截面的測(cè)量,因?yàn)轫斆媸怯芍丿B的排放坑組成,比拋光的橫截面表面更粗糙。
對(duì)于所有的EDM表面,在重鑄層中可以觀察到顯微硬度的顯著增加。這首先歸因于重鑄層獨(dú)特的致密微觀結(jié)構(gòu)。第二個(gè)原因是材料成分的變化(碳和氧含量的增加),這將在下一節(jié)中進(jìn)行討論。
A.3.3. 材料成分分析
圖A.6顯示了在五個(gè)加工步驟(R2、R5、F10、F1和F5)下生成的表面的材料組成信息。給出了每個(gè)材料元素的歸一化重量百分比,以表征與機(jī)加工表面不同深度的材料成分的變化。
對(duì)于R2和R3(步驟1和步驟2)的加工表面,在圖A.6中觀察到碳和氧含量的顯著增加。在機(jī)加工表面上,氧氣增加約18倍,碳含量增加約7倍。對(duì)于r2和r3表面,經(jīng)歷材料成分變化的層的深度分別小于5μm和3μm。這比重鑄層的厚度要薄。它被認(rèn)為是材料成分的變化僅被限制在重鑄層內(nèi)。圖A.7(a)和(b)比較EDM粗糙處理后基礎(chǔ)材料和已加工表面的EDS光譜。氧和碳元素的峰值上升表明了這兩種材料成分的增加。機(jī)加工表面頂部的峰值氧組成是基礎(chǔ)材料的10倍以上。氧氣的增加是由于氧加工介質(zhì)和氧化過程的促進(jìn)EDM過程中氧含量的遷移。在粗加工過程中,除了原始材料中的碳(小于1%)外,碳含量的增加還存在爭(zhēng)議。一種可能的解釋是,在材料的熔化和凝固過程中發(fā)生了碳分布的重排。低分子量的碳含量在重鑄層的上部漂浮并積累。
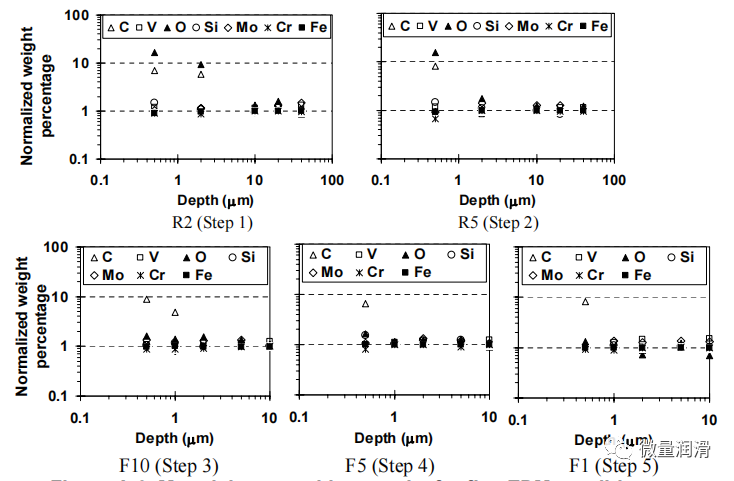
圖A.6。五種EDM條件下的材料組成結(jié)果。
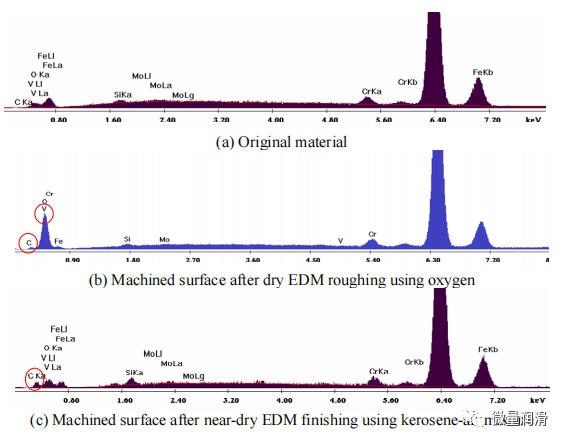
圖A.7。EDM粗糙、精加工前后H13工具鋼的EDS光譜。
氧氣和碳含量的增加都有助于提高材料的顯微硬度。增加碳量有助于提高鋼材料的耐磨性和表面耐磨性(Kruthetal.,1995),氧元素使材料變硬,但也易脆(Emsley,1998)。此外,額外的碳和氧元素的展示也表明了分解和蒸發(fā)導(dǎo)致基材料元素的損失。鉻的損失是最顯著的,它可以降低機(jī)加工表面的耐腐蝕性。還觀察到鐵元素的某些損失。
對(duì)于f10、f5和f1產(chǎn)生的表面,碳含量的增加(約為增加的8倍)是最顯著的。在圖A.5中,觀察到碳成分增加到基礎(chǔ)材料成分的8倍。由于接近干燥的EDM使用煤油-空氣混合物,額外的碳含量應(yīng)該來(lái)自分解的煤油,一種碳?xì)浠衔镉?Kruth等。1995)。F10加工表面的碳含量增加的層厚約為2μm,F(xiàn)5和F1加工表面的厚度小于1μm。碳含量的增加有助于提高重鑄層的顯微硬度。
A.3.4. 表面殘余應(yīng)力分析
圖a.8顯示了一對(duì)具有不同入射角的光束ψ和衍射角2θ的XRD光譜。根據(jù)2θ位移和方程A.1,可以計(jì)算出表面殘余應(yīng)力。
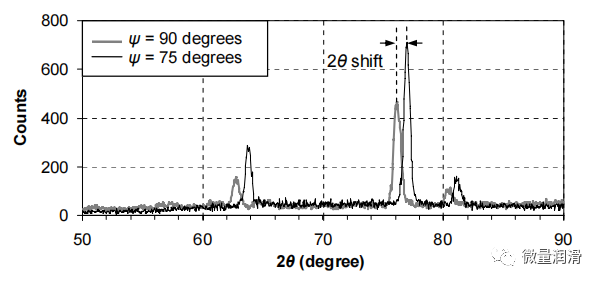
圖A.8。在不同的光束入射角度下測(cè)量的XRD光譜。
計(jì)算得到的應(yīng)力為467±561MPa。結(jié)果表明,該結(jié)果變化異常大,使得材料的屈服應(yīng)力與壓縮應(yīng)力區(qū)域之間的測(cè)量范圍發(fā)生了變化。它顯然不能給出對(duì)殘余應(yīng)力狀態(tài)的準(zhǔn)確判斷,即使識(shí)別拉伸應(yīng)力是符合預(yù)期的。
巨大的變化實(shí)際上是由于可用的XRD設(shè)備的限制造成的。假設(shè)測(cè)量誤差僅來(lái)自2θ識(shí)別,通過對(duì)方程A.2的方差分析,可以得到應(yīng)力測(cè)量的方差σ2(σφ):

,σ2(σφ)和σ2(σφ)分別是2θn和2θi測(cè)量的方差,和K被認(rèn)為是常數(shù),因?yàn)樗蝗Q于無(wú)應(yīng)力材料特性和ψ的設(shè)置,這是固定的在每個(gè)測(cè)量,我們假設(shè)每個(gè)重新定位ψ有很好的重復(fù)性。方程A.2表明,2θ識(shí)別精度高,K值較小,測(cè)量變化較小。XRD設(shè)備的最小θ定位分辨率為0.02度,具有一般的XRD應(yīng)用能力,因此2θ識(shí)別的最佳精度為0.04度。從方程B.1可以看出,特定測(cè)試材料的K依賴于θ和ψ。大θ和大ψ有助于產(chǎn)生小k。對(duì)于應(yīng)力測(cè)量,ψ角度更好為0到90度,而當(dāng)前設(shè)備的最大ψ為20度。至于θ,它是非應(yīng)力材料的理論衍射角,由布拉格定律確定:

,其中d為反射平面的晶格間距,是非應(yīng)力材料的性質(zhì),隨平面指數(shù)變化,λ為入射x射線的波長(zhǎng),該波長(zhǎng)由x射線產(chǎn)生的目標(biāo)材料決定。檢查鐵素體和馬氏體鋼工件,(211)平面和Cr的組合推薦目標(biāo)或(220)飛機(jī)和Co目標(biāo)(BrukerAXSInc.,1999)。然而,銅是目前XRD設(shè)備中唯一可用的目標(biāo)。Cu目標(biāo)產(chǎn)生的x射線波長(zhǎng)比Cr和Co的波長(zhǎng)短,θ更小。結(jié)合所有這些因素,可以通過方程中的方差計(jì)算估計(jì)不同目標(biāo)材料和ψ設(shè)置下的應(yīng)力測(cè)量誤差A(yù).2.表A.1總結(jié)了估計(jì)結(jié)果??梢钥闯?,目前的XRD設(shè)置,Cu目標(biāo),在測(cè)試材料的(221)平面和20度的ψ上,產(chǎn)生了令人難以接受的大測(cè)量誤差,接近800MPa。因此,建議進(jìn)行進(jìn)一步的研究,以實(shí)現(xiàn)更好的殘余應(yīng)力測(cè)量,使用XRD系統(tǒng),可以提供更長(zhǎng)的波長(zhǎng)x射線和更大的ψ角度調(diào)整或殘余應(yīng)力測(cè)量的替代方法,如中子衍射、盲孔鉆孔等。
表A.2。應(yīng)力測(cè)量誤差的估計(jì)(MPa)。
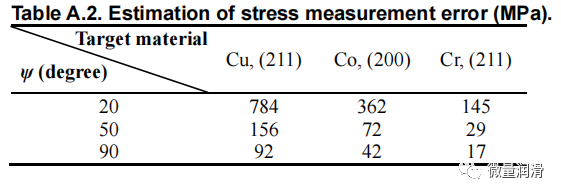
A.4. 結(jié)論性言論
本章表征了干燥和接近干燥的EDM加工對(duì)機(jī)加工表面性能的影響,包括重鑄層形態(tài)、顯微硬度和材料組成。重鑄層沒有明顯的微觀結(jié)構(gòu)模式。在粗糙加工過程產(chǎn)生的表面上存在微裂紋,并在精加工過程中減小。重鑄層的厚度為從粗糙加工減少到精加工工藝。EDM表面的顯微硬度較高。重鑄層的顯微硬度是基礎(chǔ)材料的兩倍。獨(dú)特的顯微結(jié)構(gòu)和材料組成的變化歸因于顯微硬度的密集增加。硬度增加的層延伸到重鑄層的下方,表明EDM表面存在熱影響區(qū)。在EDM表面檢測(cè)到材料成分的變化,僅在重鑄層內(nèi)。干氧電火花加工的表面氧和碳含量增加。使用煤油-空氣混合物,接近干燥的EDM產(chǎn)生的表面碳含量增加。
隨著向加工過程過渡,表面完整性提高,對(duì)材料性能變化的影響減少。受電火花加工影響的材料層的厚度小于2μm(按F1計(jì)算)。
在最終成品表面檢測(cè)到張力殘余應(yīng)力,但由于設(shè)備的限制,無(wú)法確定確切的應(yīng)力值。發(fā)現(xiàn)具有長(zhǎng)x射線波長(zhǎng)、大ψ調(diào)整的XRD系統(tǒng)可以實(shí)現(xiàn)準(zhǔn)確的測(cè)量。